Redwood Materials is Building an Electric Vehicle Battery Recycling Facility in South Carolina
【Summary】Electric vehicle battery recycling startup Redwood Materials announced its building a battery recycling facility in South Carolina. The facility will support the region’s emergence as a growing EV and battery manufacturing hub. The company collects end-of-life batteries and extracts valuable raw materials such as nickel, copper, cobalt, and lithium, which are then used to manufacture cathode and anode materials for new batteries.
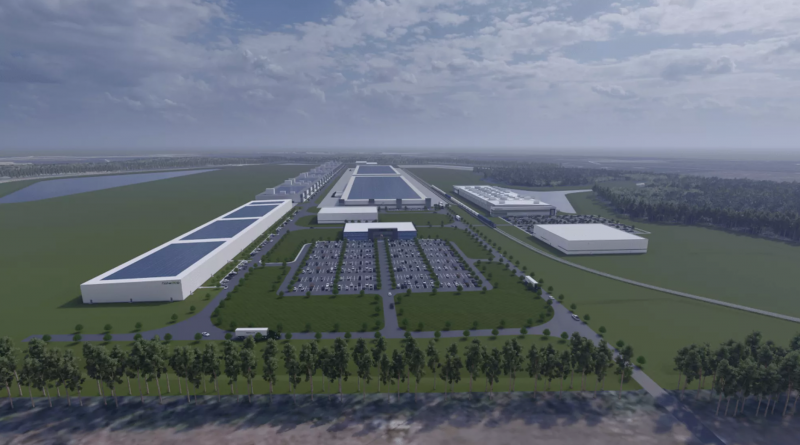
Electric vehicle battery recycling startup Redwood Materials announced its building a battery recycling facility in South Carolina. The facility will support the region's emergence as a growing EV and battery manufacturing hub.
Nevada-based Redwood Materials plans to break ground on its new 600-acre South Carolina Campus in Q1 2023 and have the first recycling process running by the end of 2023. The plant will create more than 1,500 new jobs.
Redwood Materials combines recycling, refining and remanufacturing to produce and return battery materials to U.S. battery cell manufacturers. The company collects end-of-life batteries, and extracts valuable raw materials such as nickel, copper, cobalt, and lithium. These recycled materials are then used to manufacture cathode and anode products that will go into new batteries.
Redwood says its EV battery recycling technology can recover, on average, more than 95% of the elements like nickel, cobalt, lithium and copper from a battery. Once recycled these materials can be reused to produce anode copper foil and cathode active materials for future battery production.
Redwood's new facility in South Carolina is an ideal location to serve the auto industry. Automakers Hyundai Motor Co, Kia, Volvo, BMW and Mercedes Benz are investing billions to build EV factories in the Southeast U.S., as well as battery manufacturing facilities.
The region just outside of Charleston, South Carolina is often referred to as the "Battery Belt." Redwood estimates that hundreds of GWh a year ofbattery cell production capacity will be operational in the region by 2030 to supply automakers.
Redwood aims to produce 100 GWh of cathode and anode components a year, which is enough to manufacture the batteries for over million EVs. The plant is also designed for future expansion. Redwood says it potentially can produce several hundred GWh of anode and cathode materials to meet future demand.
Redwood Materials was founded in 2017 by J.B. Straubel, one of the co-founders of electric automaker Tesla along with Martin Eberhard and Marc Tarpenning. The three launched Tesla before current Chief Executive Elon Musk, who was an early investor, joined the company.
Straubel served as Tesla's first Chief Technical Officer and was the automaker's fifth employee. He worked for Tesla until 2019, but launched Redwood Materials in 2017 while still working for the electric automaker.
Speaking at a conference in Oct 2020, Straubel said he wants to build Redwood Materials into "the world's top battery recycling company."
In 2019, Tesla's battery partner Panasonic entered into a partnership with Redwood Materials to reclaim the scrap generated from battery cell production at Tesla's gigafactory in Nevada. Currently all of the scrap materials left over from battery production is shipped to Redwood's Nevada facility for recycling.
One of the goals of recycling of used EV battery materials is to help drive down the high cost of producing them. The high cost of batteries is one of the reasons that most EVs cost thousands of dollars more than similar gas-powered vehicles. Battery manufacturers that are using a steady supply of recycled raw materials can also help address growing demand for batteries as the world's automakers transition to building more EVs.
Redwood believes that in order to make electric vehicles sustainable and affordable, pathways for the collection, recycling and remanufacturing end-of-life battery packs into new battery materials need to be established.
Currently, most of the anode and cathode components for EV batteries are produced overseas, predominantly from China and South Korea. As a result, battery cell manufacturers have to source them via a 50,000+ mile global supply chain.
Redwood estimates that battery manufacturers will spend more than $150B on anode and cathode materials produced overseas by 2030. This sends most 50 to 75% of the economic value and job creation to outside of the U.S., according to Redwood. In order to reduce the reliance of overseas suppliers, metals such as lithium and nickel will need to be produced and refined locally.
In March, Redwood Materials announced the launch of a comprehensive battery recycling program in California to efficiently and safely recycle end-of-life hybrid and electric vehicle battery packs. Automakers Ford Motor Co and Volvo Cars were the first automakers to directly support the program. Redwood Materials says it will accept all lithium-ion (Li-ion) and nickel metal hydride (NiMH) batteries in the state and welcomes other automakers to join in its recycling efforts in California.
Redwood Materials also announced a separate collaboration with Toyota in July for the recycling of EV batteries. The two companies plan to build an entire closed loop ecosystem for the recycling batteries from Toyota's future hybrid and fully-electric vehicles.
-
Ford is Testing a New Robotic Charging Station to Assist Drivers of EVs With Disabilities
-
Ford Raises the Prices of the F-150 Lightning Electric Pickup Due to Rising Raw Material Costs
-
The BMW 7-Series to Feature HD Live Maps From HERE Technologies for Hands-Free Highway Driving in North America at Speeds up to 80 MPH
-
AutoX to Use the 'Eyeonic Vision Sensor' from California-based SiLC Technologies for its Robotaxi Fleet in China
-
LG Develops ‘Invisible’ Speaker Sound Technology That Could Revolutionize In-Vehicle Audio
-
Researchers at South Korea’s Chung-Ang University Develop a ‘Meta-Reinforcement’ Machine Learning Algorithm for Traffic Lights to Improve Vehicle Throughput
-
Zeekr’s New 009 Electric Passenger Van is the World’s First EV to Feature CATL’s Advanced ‘Qilin’ Battery With a Range of 510 Miles
-
Panasonic Announces Multi-Year Agreement to Supply Electric Vehicle Batteries to Lucid Group
- Foxconn-led Mobility in Harmony Consortium Announces ‘Project X’, an Open, Modular Electric Vehicle Platform
- Construction of Panasonic’s New EV Battery Factory in Kansas to Start in November
- Volvo-backed EV Battery Maker Northvolt, Founded by Former Tesla Execs, Raises Another $1.1 Billion to Help Fund its Expansion
- SK Inc. Invests $100 Million in North Carolina-based EV Charging Hardware Developer Atom Power
- Electric Hypercar Developer Rimac Raises $500 Million Euro in Series D Round, Investors Include Porsche, Softbank and Goldman Sachs
- Hyundai Motor Group Signs MoU with SK On Co. to Secure Batteries for EVs Built in the U.S.
- China’s Tesla Rival XPeng Unveils its New ‘S4’ 480kW Electric Vehicle Supercharger That Can Add 125 Miles of Range in Just 5 Minutes
- LiDAR developer Luminar Technologies Hires Ex Apple, Tesla and Nvidia Execs as it Prepares for Growth
- Lucid Group Hires Key Executives that Formerly Worked for Mercedes-Benz and Tesla as it Prepares for Global Expansion and Production Ramp Up
- Tesla May Build its Next Factory in South Korea, According to the Country’s Presidential Office