Building a Better Battery
【Summary】Renewably powered electric vehicles will change the world, but the EV battery is one of the biggest things standing in the way of widespread consumer adoption. The race is on to build a better battery. Here we will explore some of the ways people are working to build a better battery.
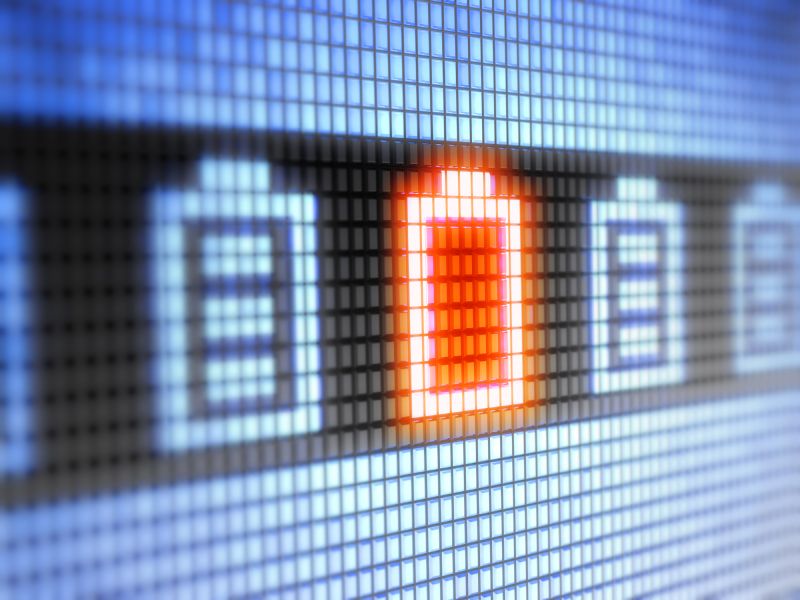
Renewably powered electric vehicles (EVs) will change the world. One of the largest barriers to the adoption of electric vehicles (EVs) over cars with an Internal Combustion Engine (ICE) centers on the battery, including the cost of the battery and the range available from the battery. For widespread adoption of EVs, the experience will need to be similar to that of a traditional vehicle. This is accomplished by equalizing or exceeding on Price and Performance:
• EV sticker prices should meet or beat ICEs
• Eliminating range anxiety by
▪ increasing the capacity of the batteries
▪ building an extensive charger network
▪ ensuring minimal recharge times
Much of this centers around the improvements and innovations with EV batteries.
Modern electric cars are reliant on Lithium Ion or Li-ion batteries. These batteries are far superior to the Lead Acid batteries used in traditional, ICE vehicles. Li-ion batteries have better usable capacity, extended cycle-life, size and weight advantages, fast and efficient charging, perform better in a range of environments, and are much more cost effective.
Building a better battery has the following areas for improvement -- Material Science, Cell Design and Manufacturing Process
Material Science
Batteries are quite simple in terms of their composition with four main components:
cathode (+)
anode (-)
separator - the lithium ions move through the separator material
electrolyte - the material in between the separator layers.
There are gains to be made by optimizing the combination of these materials for the battery application.
Cell Design
An individual battery, like the one you might put in your flashlight or is installed inside your mobile phone is called a cell. There are two types of cells, stacked and wound ones.
Stacked cells are flat batteries with layer after layer of separator on top of each other. This form factor is the type of battery in your laptop, digital camera, etc… Stacking layers is done by hand or robot.
Wound cells are round batteries where the separator is rolled up. The layers are rolled by machine, which is considerably faster and therefore more cost effective than the Stacked cells. Both formats can be created in a range of different sizes. Regardless of the type of cell form factor, temperature control through proper venting is a necessity.
Manufacturing Process
Having the perfect combination of materials and efficient cell design is not enough. The manufacturing process must be able to produce the units precisely and quickly. One of the issues with the second Samsung Galaxy Note 7 battery (pulled from the market after infamously overheating and catching fire) was that as the battery supplier rapidly increased production to meet urgent demand, a welding defect was introduced — a defect which was then repeated at scale.
Advances in material science, cell design and the manufacturing process can improve any type of battery use case. In the case of electric vehicle batteries, there is also the configuration of the batteries to optimize. It is not currently feasible to have a single large battery in an electric vehicle. The current design is to create battery packs which are essentially an array of batteries assembled into a larger unit. Optimization can occur by packing the cells in the most efficient and effective manner based on the goals of the vehicle.
Cell packing
Within the individual battery pack, how does one control the temperature of the batteries, what is the physical protection or packaging and what are the interconnections? How these packs are designed and arranged has an impact on both the performance and the physical design of the vehicle. How much power can one get out when the driver needs it? How long can one drive without recharging? How long will it take one to fully charge? How does one accommodate the vehicle around the battery arrays and powertrain? We are relatively early in the life of electric vehicles and no one has won this area yet. As batteries improve, cell packing will be modified and improved to match the new possibilities and requirements.
Battery advancements for EV Lithium-ion batteries
Current innovation is focused largely on new materials in the battery components. Examples of this include graphene as a conductive binder, electrolytes that are less fire prone, and silicon-alloy anodes for more energy density.
Increased capacity
One company that is moving the needle is Amprius. Based in Sunnyvale, California with additional R&D in Tianjin, China, and a factory in Wuxi, Jiangsu, China, Amprius has innovated the manufacturing process for a newer anode (-) material. Anodes have traditionally been carbon based, namely graphite (yes, like in your pencil). Silicon offers 10 times more energy than carbon, but the substance also expands and breaks. In order for the silicon to be more resilient, the substance needs to be modified and the resulting process needs to be scalable, making commercial use viable. Stanford University Materials Science and Engineering worked on this over several years and developed a fabrication technique called in situ synthesis polymerization. This process coats the silicon nano particles within the conducting hydrogel.
The end products are batteries that are able to achieve higher energies per unit volume and per unit weight than the current set of batteries that are available commercially. Amprius refined this solution into a commercially viable manufacturing process and unveiled its manufacturing tool in Summer of 2016. Their batteries are now being produced for drones, wearables and electric vehicles.
Increasing range
DCB Power (Dual Chemistry Battery) was co-created by Nad Karim, the idea is not a better battery, but a battery system. A vehicle with DCB Power technology would have two battery packs, each with very different properties. The battery packs would also be utilized at the appropriate time to optimize the vehicle's range. This would result in a range increase of up to 50 percent for the same cost and weight of a traditional EV battery system. This was conceived and documented in 2011 and the patent was granted in December 2016.
The Chevy Volt, a hybrid car, uses a similar system. The Volt has a battery with a 40 mile range and is recharged by a gas powered generator when the battery is close to being depleted. The DCB power system would have a main, (40 mile range) battery similar to the Chevy Volt in principle, which is used in general for all motive and regenerative requirements until it is depleted. Then the supplemental pack is used as a backup battery pack for occasional use when required.
Note: The 40 mile range is a typical baseline as the average American drives just 32 miles per day, so it would be possible for most Americans to drive completely on electricity on a regular basis.
Why does Dual Chemistry Battery Power work? EV batteries are not fully utilized in electric-vehicle applications. According to Karim, only 60 to 70 percent of the energy within batteries in electric vehicles is used. This is because the state of charge of the battery affects its performance. If the battery is above 90 percent or below 20 percent, the battery gets harder and harder to charge or discharge as the impedance or resistance to electrical energy flow increases. This causes the battery to heat up, makes it less efficient and damages the battery. For example, Tesla recommends that you do not charge your battery to 100 percent unless you know you really need the range. If the driver doesn't need to travel 280 miles, drivers should charge the vehicle to give it a range of 200 miles. This will not only give owners a better battery life, but it will also help the vehicle not be weighed down by the weight of a battery that will not be used completely.
With DCB power, the two batteries are of different profiles. The main battery is similar to a grid power battery — one can charge it to 100 percent nearly endlessly and it may take 20 years to degrade to any appreciable level in a typical car. The supplemental battery is a larger, lower cost battery, that would typically be sized to provide the range the car manufacturer desires. So the main pack would offer the vehicle an additional range of 100 or 200 miles. This configuration allows the vehicle to carry a battery that can be used to its full potential and is more efficient, wasting less energy as heat.
Initial testing indicates an increase in range of up to 50 percent for the same cost and weight of traditionally configured EV batteries. Meaning your Tesla could go 300 miles rather than 200 if it were utilizing the DCB power configuration.
Alternatively there could be a significant cost savings if range is not extended. "If the DCB power system was implemented in a small car such as a Leaf, it would save around $2300 in battery cost, providing the same range. However for a larger car such as a Tesla that number could be $16,000," Karim stated. This would also decrease the weight of the battery pack by one-third.
Safer, longer lasting batteries
Current lithium-ion batteries are potentially dangerous. A chemical reaction is occurring between the liquid electrolyte and the electrodes to create the energy. The higher energy the battery has, the more likely it will catch fire if not managed properly. Pure lithium metal electrodes would be very high energy, but can react with liquid electrolytes generating dangerous amounts of heat. Creating a safe, high energy battery is a holy grail for the battery world. Large corporate, startup and university teams around the world are all working on such solutions.
Sustainability improvements
Traditional lead acid car batteries are poisonous. The smelting and extraction process that leads to lead being put inside traditional batteries is terrible for the environment. In addition it can poison workers and have a negative impact on brain development. Sulfuric Acid is highly corrosive and dangerous to handle, as well. It's so bad that China is considering banning all lead-acid batteries. As awful as these batteries are, they are very inexpensive and recycling is generally successful with between 96 percent and 99 percent of the battery components being reused or recycled.
Conversely Lithium-ion battery components are plentiful and non-toxic, but there is no established system for recycling Li-ion automotive batteries. This is largely due to the lifespan of the batteries and their novelty in the market. Many Li-ion automotive batteries are thought to be able to last the life of the vehicle. When they are no longer sufficient for an automotive application, they can be reused for storage. EV batteries may still have 70 to 80 percent of their life remaining when they are deemed too poor for the vehicle.
Examples of this second-life EV battery technology are the Tesla Powerwall and Freewire Technologies. Tesla Powerwall is a power storage system that can be used in conjunction with solar panels for home energy storage and vehicle charging. Freewire Technology bundles used automotive battery packs into a block configuration to create portable power generators or mobile vehicle chargers. These can then be deployed anywhere gas generators are typically used. In addition, they have utilization and tracking technology that is not currently available in combustion engine portable power.
When these Lithium-ion batteries have finally met their end and there is a critical mass of spent Li-ion batteries, it is certain that the recycling and disposal systems will be in place to minimize environmental impact. Until then, increasing the power and energy in every battery produced is a much higher priority for the industry.
- Border collision: New York driver crashes into Canadian territory
- Tesla's triumph over Swedish labor unions and government in battle for business.
- Electric Nissan Juke And Qashqai Get Inspiration From Cutting-Edge Concepts
- Lancia Replica Features Alfa Romeo V6 and Manual Transmission
- Dodge Magnum SRT-8 Up for Auction
- AI's Influence on Automotive Design
- Forecaster reduces 2027 electric vehicle sales forecast
- Global Automakers Seek Electric Vehicle Insights from China
- Canadian border Niagara Falls New York businessman motorist ploughed
- Hyundai Ioniq 6 N: Unleashing Superior Power